Understanding Tooling Die Casting: A Game Changer for the Metal Fabrication Industry
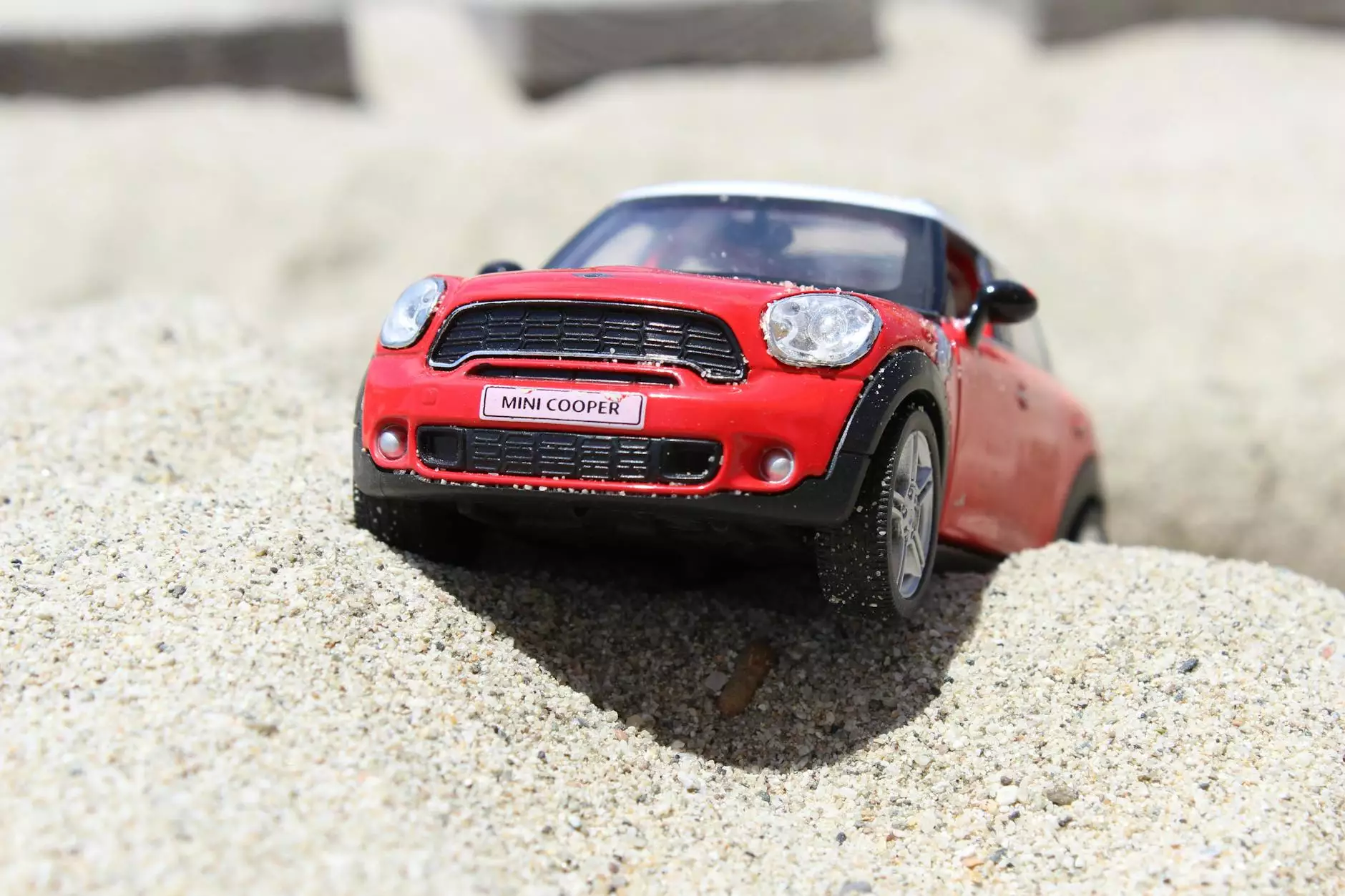
In the fast-evolving landscape of manufacturing, tooling die casting has emerged as a pivotal technique that enhances productivity, quality, and cost-efficiency. This article dives deep into the fundamentals and advantages of tooling die casting, presenting essential information for businesses looking to leverage this technology in their operations.
What is Tooling Die Casting?
Tooling die casting is a manufacturing process that involves the injection of molten metal into a mold to create precise, complex shapes. This method is particularly favored in industries requiring high-volume production of intricate components, such as automotive, aerospace, and electronics.
The Process of Tooling Die Casting
The die casting process consists of several key stages:
- Preparation: The first step involves preparing the die, made from steel or other durable materials, which is engineered to withstand high temperatures and pressure.
- Melting: The metal, often an alloy of zinc, aluminum, or magnesium, is melted in a furnace to achieve the required temperature for casting.
- Injection: Once melted, the liquid metal is injected into the mold at high speed and under pressure, ensuring that it fills every cavity in the die.
- Cooling: After injection, the molten metal is allowed to cool and solidify, taking the shape of the die.
- Removal: Finally, the mold is opened, and the finished component is ejected for further processing, which may include trimming and finishing.
Benefits of Tooling Die Casting
Tooling die casting offers numerous advantages, making it an attractive option for metal fabricators:
- High Precision: The process allows for the production of parts with tight tolerances, ensuring consistent quality and reducing the need for further machining.
- Complex Geometries: With the ability to create complex shapes, tooling die casting is suitable for intricate designs that are difficult to achieve with other manufacturing processes.
- Durability: Components produced through die casting often exhibit high mechanical strength, making them ideal for demanding applications.
- Cost-Effective: While the initial investment in dies can be significant, the high-speed production rate results in lower per-unit costs for large runs.
- Material Efficiency: Die casting minimizes waste, as it typically requires less machining, and the excess metal can often be recycled.
Applications of Tooling Die Casting
Tooling die casting is utilized across a variety of industries, including:
- Automotive: Used for manufacturing engine blocks, transmission cases, and other high-strength components that require precision.
- Aerospace: Essential for producing lightweight yet robust parts that meet stringent safety and performance standards.
- Electronics: Commonly used for creating enclosures and components with intricate designs that offer shielding and aesthetics.
- Consumer Goods: Employed in the production of high-quality, durable appliances and tools.
Choosing the Right Metal Fabricator
When considering tooling die casting for your manufacturing needs, selecting the right metal fabricator is crucial. Here are some factors to consider:
- Experience: Look for a fabricator with a proven track record in tooling die casting to ensure quality and expertise.
- Technology: A modern factory equipped with state-of-the-art machinery can greatly enhance production capabilities and quality.
- Customization: Choose a partner that can tailor solutions to meet your specific design and production requirements.
- Quality Assurance: Ensure that the fabricator employs stringent quality control measures to maintain high standards.
- Customer Support: Effective communication and support throughout the project lifecycle are essential for successful partnerships.
The Future of Tooling Die Casting
As technology advances, the future of tooling die casting looks bright. Innovations such as:
- 3D Printing: Integrating 3D printing with die casting can allow for faster prototyping and tooling changes, significantly reducing lead times.
- Smart Manufacturing: The implementation of IoT and AI in die casting processes can enhance efficiency through predictive maintenance and process optimization.
- New Alloys: Ongoing research into new metal alloys can expand the capabilities of die casting, allowing manufacturers to create lighter, more durable parts tailored to specific applications.
Conclusion: Harnessing Tooling Die Casting for Business Growth
In conclusion, tooling die casting represents a vital manufacturing process for businesses in the metal fabrication industry. Its ability to produce high-precision, complex components at scale offers unparalleled advantages for a range of applications. As you consider integrating tooling die casting into your operations, understanding its benefits, applications, and the factors influencing your choice of fabricator is crucial for maximizing the potential of this technology.
At DeepMould.net, we specialize in not just meeting your tooling die casting needs but exceeding your expectations through quality, innovation, and customer service. Embrace the future of manufacturing with us, and together we can unlock greater possibilities for your business.